Start Date: 2012
Project Duration: 24 months
The thought to construct a CNC machine has come to my mind already during my years of study. However, at that time there were no possibilities to do it. Finally when the opportunity to realize that thought has opened I had to consider a couple of possible options:
- To buy a ready-made machine (made in China) or
- To construct the machine myself that would mean spending much more time and money, however, at the same time, gaining much more knowledge and experience. I have decided to go with the second option. Apparently, the future creative struggles seemed very tempting. The project had been started in 2012 and finished in 2014.
The goal of this project was to have a CNC machine that would allow me to process wood, plastics and soft metals with a less than 0.05mm margin of tolerance. Being as environmentally friendly as possible was also taken into consideration trying to reduce noise and prevent dust emissions.
The very first step was to grasp how the SolidWorks engineering software functions. The design of the CNC machine was my first project carried out using this software.
The phase of learning to use the SolidWorks and designing the machine took about 3 months.
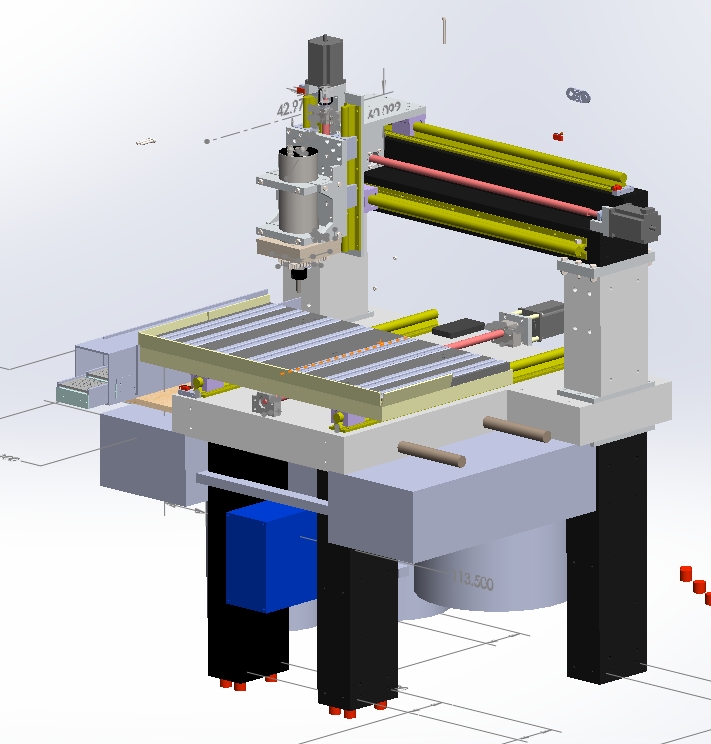
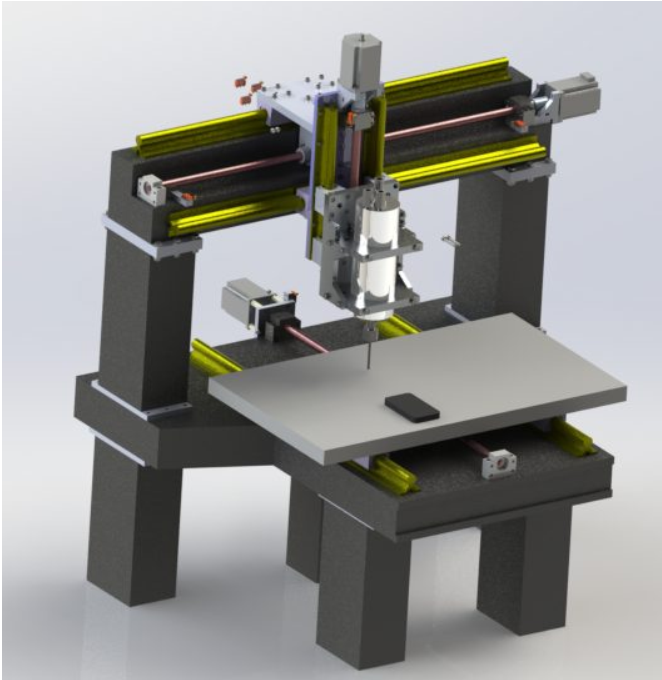
In order to achieve the highest possible rigidity of the machine, I’ve decided to make the frame from the Epoxy Granite (mixture of epoxy adhesive and granite). The modular construction offers the possibility to transport the machine, if necessary.
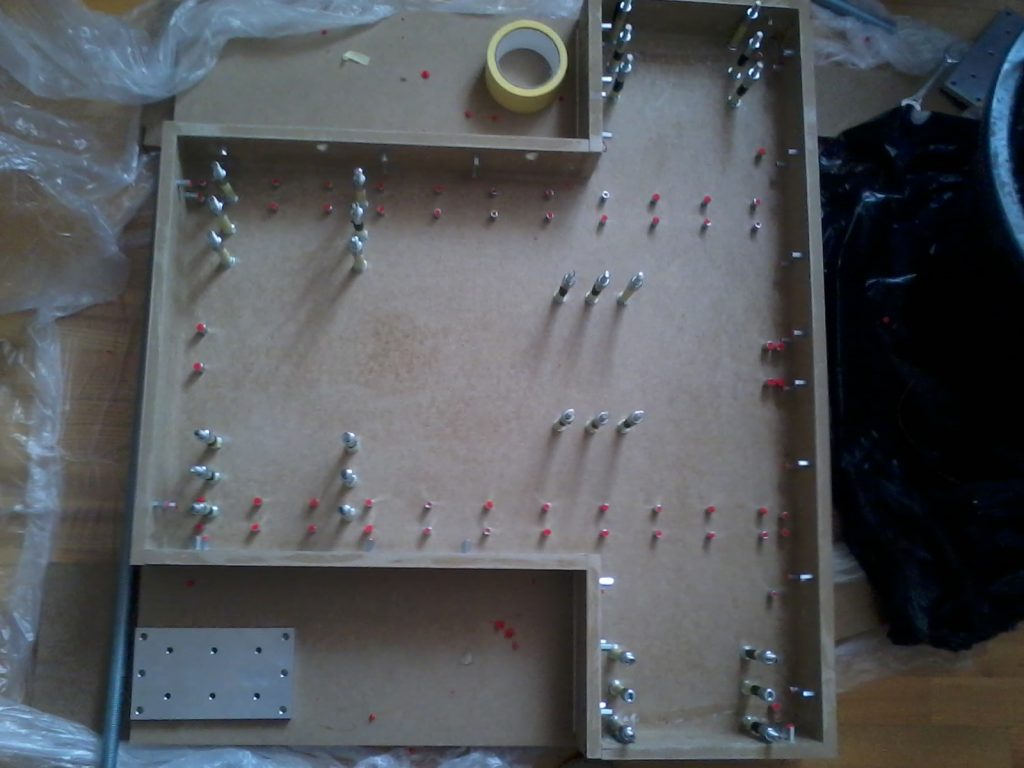
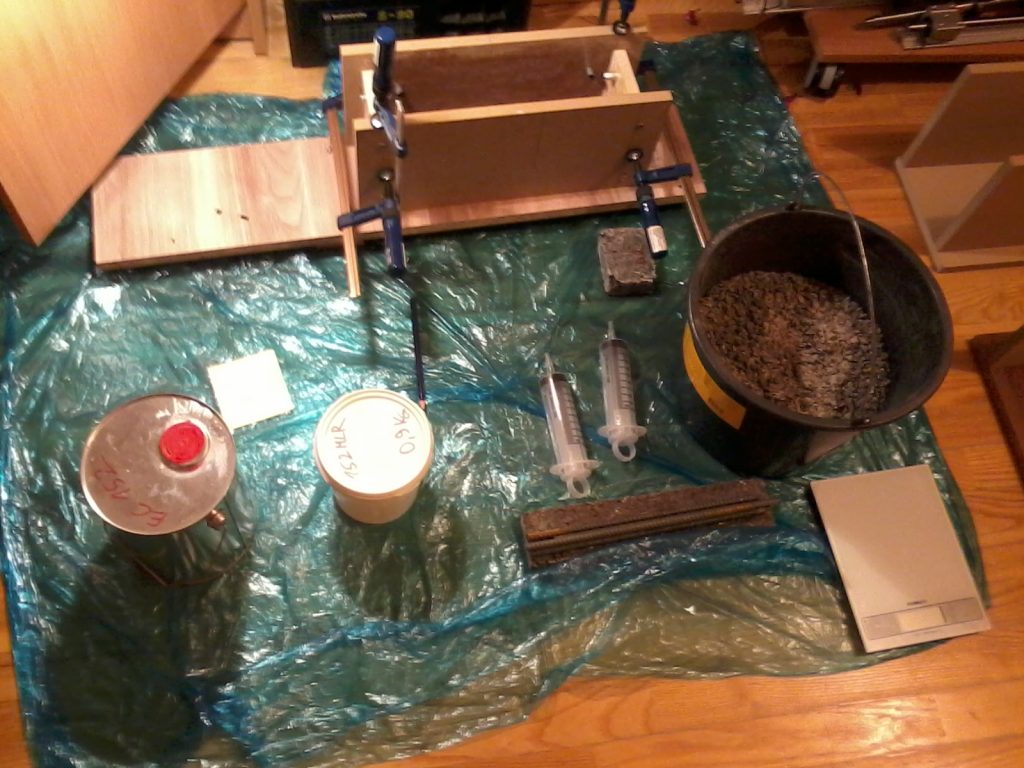
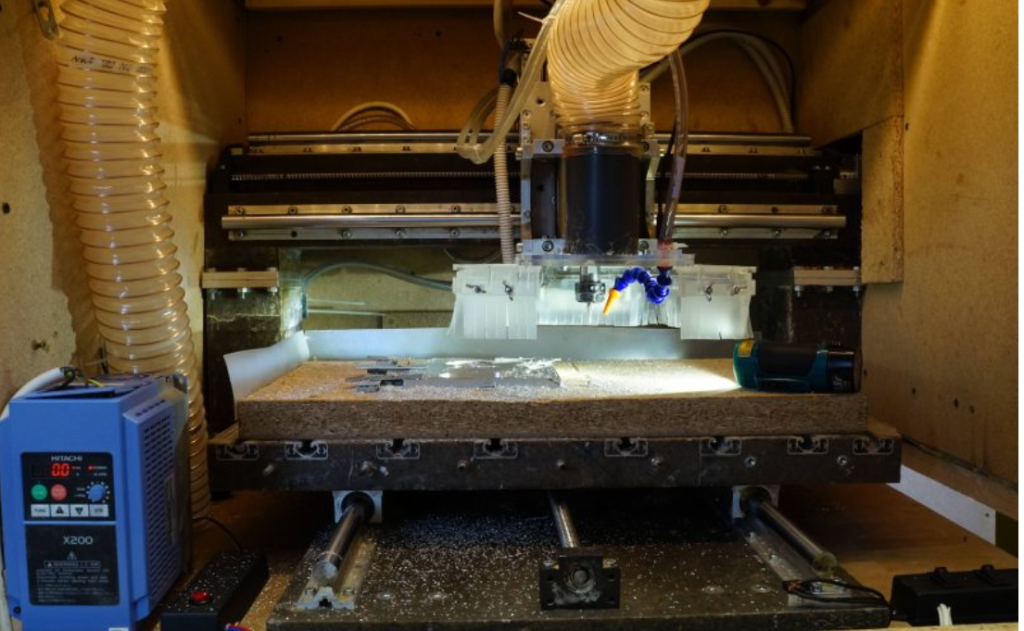
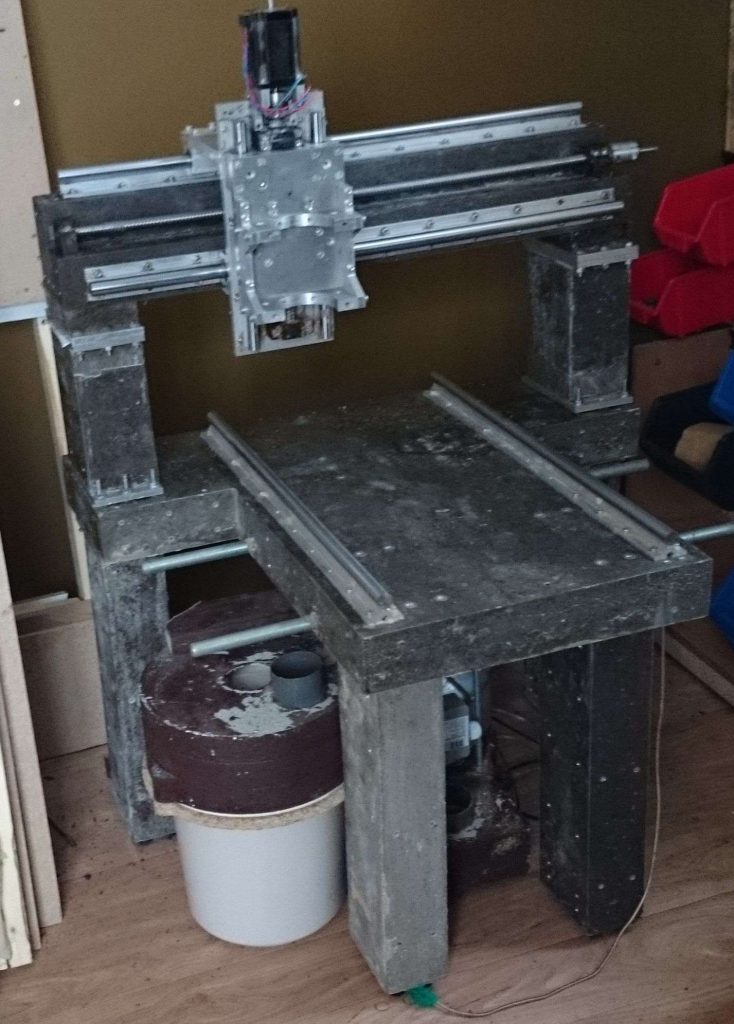
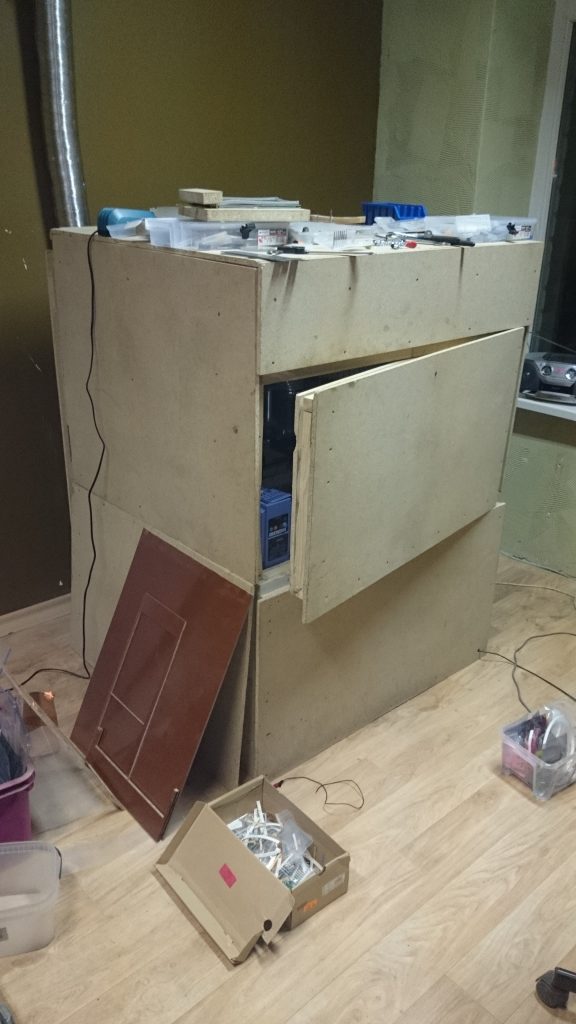
Some Key Features of the CNC Machine:
- 2.2kw high-power spindle provides the CNC machine with the ability to carry out heavy-duty milling tasks effectively;
- Control via USB: The machine can be accurately controlled through a USB interface, making it highly user-friendly;
- CAM via SolidCAM software, ensuring high precision in the production process;
- Mach3 CNC control software compatibility;
- Epoxy granite cast frame: The CNC machine boasts a robust and sturdy structure—a frame cast out of epoxy granite. This guarantees stability and durability;
- Ability to mill aluminum;
- Dust extraction system which ensures a clean and safe working environment;
- Tool cooling with air for prevent overheating and prolongs the life of the tool;
- Fixed Gantry (moving table) offering a stable platform and high precision;
- T-Slot table top;
- A simple dust shoe;
- Air compressor was employed to blow off dust;
- A camera was used to define the precise coordinates of X and Y axis;
- A joystick was connected for the control of the machine;
- Sound insulation for reducing noise during operation and contributing to a more comfortable working environment. The noise level in the closed sound enclosure box while milling aluminium at the speed of 900mm/min (cutting 0.25mm deep) is less than 70dB
- The working size of the machine is 600 x 400 x 30 cm offering a generous space for carrying out a wide range of tasks.
- The accuracy of the machining – margin of tolerance less than 0.05 mm.